Interactive Aerial
Robotic solutions for GPS-denied, confined space environments
Unmanned Aerial Systems
Interactive Aerial is a research and development company for unmanned aerial systems. They engineered the Legacy One, a drone for internal infrastructure inspections, specifically for large confined spaces that may have a GPS-denied environment. The purpose of their industrial UAV is to streamline the inspections for companies in the Oil & Gas, Utility, and Maritime industries. This confined space drone ultimately saves the industries time and minimizing safety concerns found in traditional internal inspection methods.
Exceeded Strength Performance
Exceeded Lightweight Performance
Certified for Nuclear Inspection
CHALLENGES
composite builders & Interactive Aerial
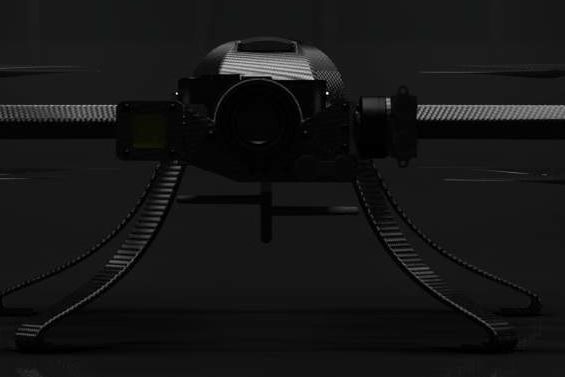
The Legacy One drone is equipped with important components for data collection and navigation. For example, it incorporates a high-resolution camera with a 180° vertically pitch, onboard lighting equipment, laser-based navigation system with integrated vertical and 360° collision avoidance systems. When developing a drone body, the weight for the flight was critical due to the load of the data and navigation equipment; these systems could not be compromised. Additionally, Interactive Aerial wanted the technical equipment encapsulated for protection.
The drone battery, large enough for a reasonable time to make an internal inspection, needed to be accessible from inside the capsule. The weight and shape of these loaded cells needed to be considered in the design of the body.
The Legacy One, charged with its technical equipment, requires a soft landing. The landing gear needed to be engineered to have lightweight and load-tolerance with ply for shock absorbance.
APPROACH
DESIGN & TOOLING
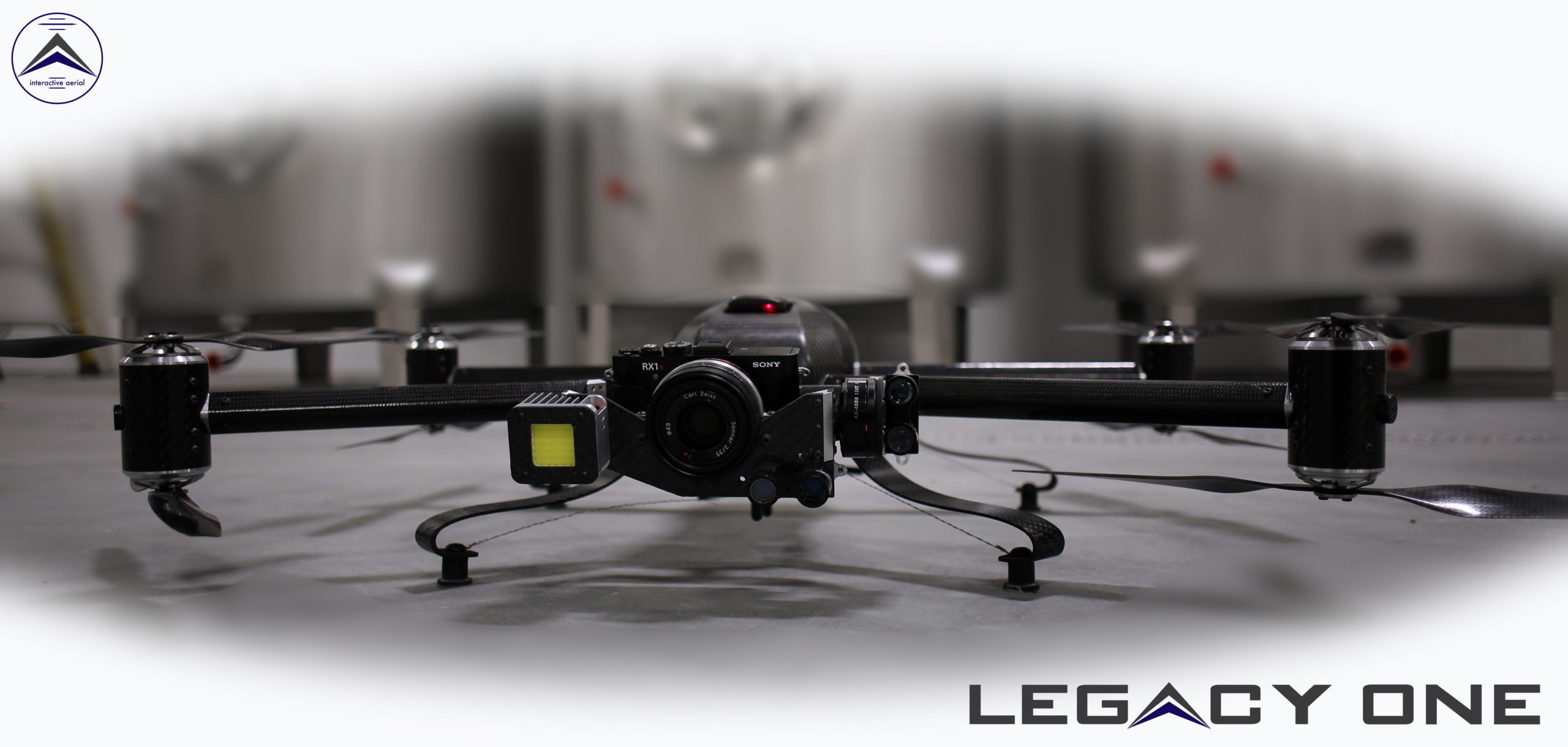
Composite Builders worked with Interactive Aerial’s engineering team to develop a capsule for the drone body. Composite Builders recommended a clamshell body with an interlocking flange on its perimeter. Interactive Aerial designed the shape of the body with the component’s internal layout, and what equipment would be mounted on its exterior. For production and repeatability, Composite Builders gave guidance on the tooling and the finished parts processing. Composite Builders created a laminate schedule with 200 gsm. twill prepreg carbon fiber, cured in our high-pressure autoclave.
The battery was secured internally with a carbon fiber case. The carbon fiber case had a laminate schedule requiring strength and an ultra-light weight.
Interactive Aerial designed a bow spring system for the landing gear. Composite Builders calculated the springs stress distribution to develop an appropriate laminate schedule.
RESULTS
STRONG & LIGHTWEIGHT
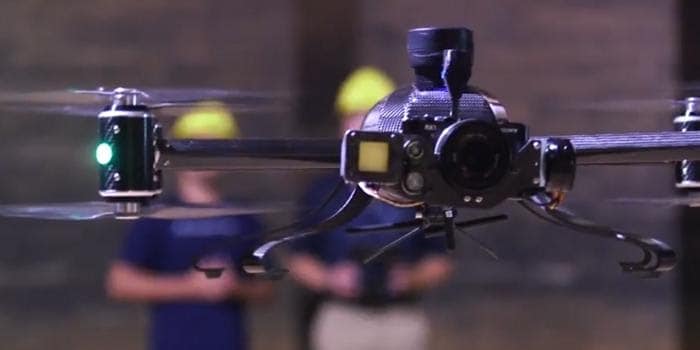
The carbon fiber components exceeded the strength & lightweight performance expected by Interactive Aerial, allowing them to increase their technical equipment capabilities. The landing gear laminating schedule was adjusted just above its shearing point to minimize unnecessary weight. Overall, the performance of the custom materials used in the drone has passed rigorous testing and The Legacy One is now certified for nuclear inspections.
Interactive Aerial has achieved their goal with the development of The Legacy One. Composite Builders maintained a given budget and timeline for prototyping and production. Cost efficiency and on-time production has allowed the Legacy One to be readily available to the industrial markets as the demand increases. With the advancements of this robotic inspection system, they have saved companies millions of dollars by eliminating traditional inspection methods, capturing critical data, saving thousands of dollars in inspection costs and downtime.
composite builders & Interactive Aerial
CHALLENGES
The Legacy One drone is equipped with important components for data collection and navigation. For example, it incorporates a high-resolution camera with a 180° vertically pitch, onboard lighting equipment, laser-based navigation system with integrated vertical and 360° collision avoidance systems. When developing a drone body, the weight for the flight was critical due to the load of the data and navigation equipment; these systems could not be compromised. Additionally, Interactive Aerial wanted the technical equipment encapsulated for protection.
The drone battery, large enough for a reasonable time to make an internal inspection, needed to be accessible from inside the capsule. The weight and shape of these loaded cells needed to be considered in the design of the body.
The Legacy One, charged with its technical equipment, requires a soft landing. The landing gear needed to be engineered to have lightweight and load-tolerance with ply for shock absorbance.
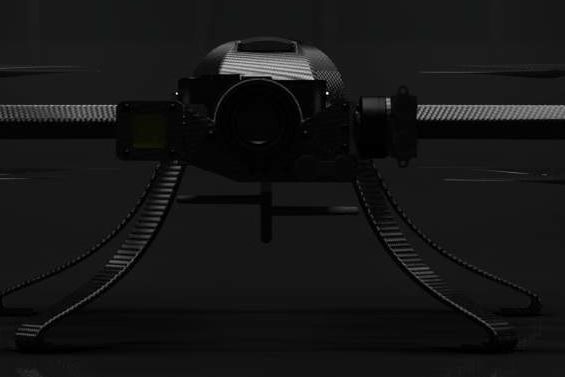
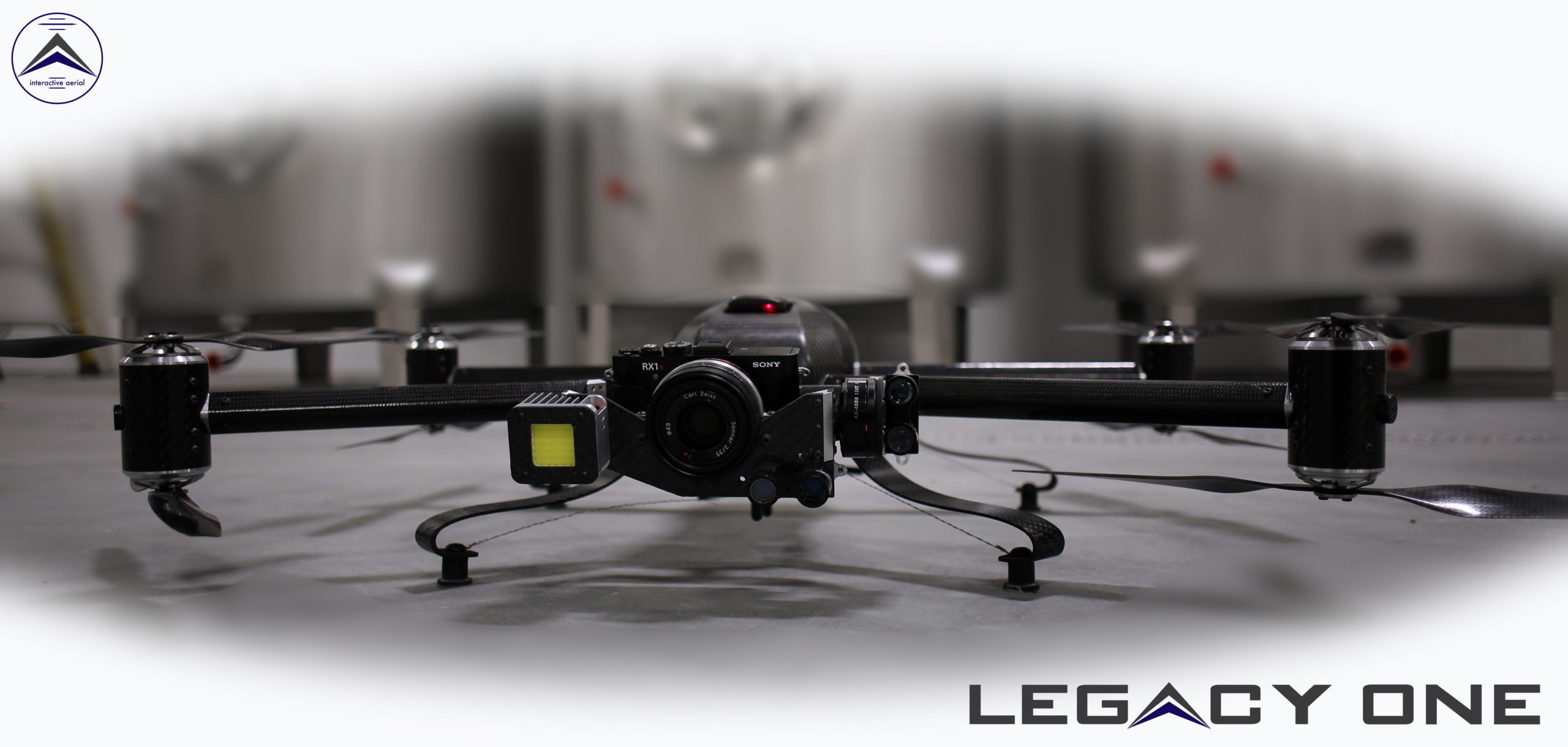
design & tooling
APPROACH
Composite Builders worked with Interactive Aerial’s engineering team to develop a capsule for the drone body. Composite Builders recommended a clamshell body with an interlocking flange on its perimeter. Interactive Aerial designed the shape of the body with the component’s internal layout, and what equipment would be mounted on its exterior. For production and repeatability, Composite Builders gave guidance on the tooling and the finished parts processing. Composite Builders created a laminate schedule with 200 gsm. twill prepreg carbon fiber, cured in our high-pressure autoclave.
The battery was secured internally with a carbon fiber case. The carbon fiber case had a laminate schedule requiring strength and an ultra-light weight.
Interactive Aerial designed a bow spring system for the landing gear. Composite Builders calculated the springs stress distribution to develop an appropriate laminate schedule.
Strong & lightweight
RESULTS
The carbon fiber components exceeded the strength & lightweight performance expected by Interactive Aerial, allowing them to increase their technical equipment capabilities. The landing gear laminating schedule was adjusted just above its shearing point to minimize unnecessary weight. Overall, the performance of the custom materials used in the drone has passed rigorous testing and The Legacy One is now certified for nuclear inspections.
Interactive Aerial has achieved their goal with the development of The Legacy One. Composite Builders maintained a given budget and timeline for prototyping and production. Cost efficiency and on-time production has allowed the Legacy One to be readily available to the industrial markets as the demand increases. With the advancements of this robotic inspection system, they have saved companies millions of dollars by eliminating traditional inspection methods, capturing critical data, saving thousands of dollars in inspection costs and downtime.
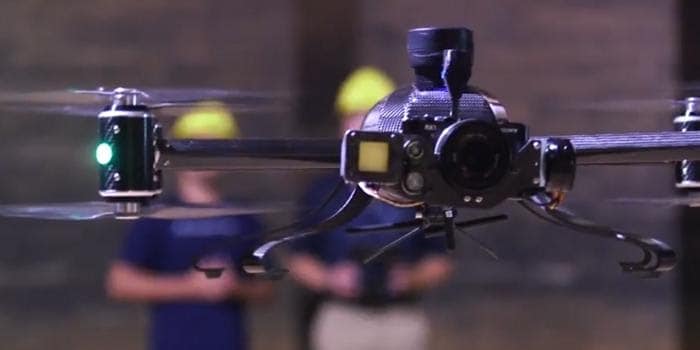
Work With Us
Tell us about your project.